高压快充,其本质就是要提高充电速度,解决用户的充电焦虑。如今普遍使用的400 V电压系统(250 A电流)可以达到100 kW的充电功率,电池由30%SOC充至80%SOC需要约30min,距燃油车的加油速度还存在很大差距,即使在未来将电流增加到500 A,也需要15min左右,而800V高压未来能达到300-500 kW的充电功率,只需几分钟就能迅速补能,可以媲美燃油车的补能速度。
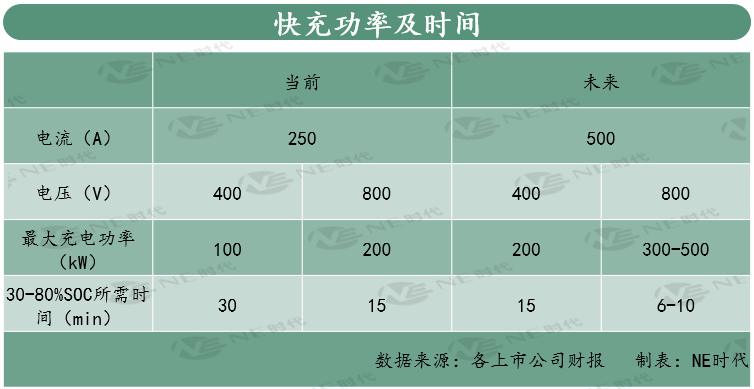
充电时间的减少在给消费者带来更好体验的同时也给电池带来了考验,电池的充电速度主要取决于锂离子的脱嵌和迁移速率,当采用800V电压平台后,充电倍率最大可达6C(目前普遍为1C),在高充电倍率下,锂离子脱嵌和迁移的速率加快,部分锂离子来不及进入正负极,只能形成一些副产物,导致活性物质损失,加速电池寿命衰减。且动力电池在快充条件下,析锂现象加剧,一方面将造成活性物质的损失,影响电池容量和寿命;另一方面,锂枝晶一旦刺穿隔膜,将导致电池内部短路,造成起火等安全风险。
为解决上述问题,业界针对电池各组分做出了大量努力:
正极材料方面,最新的亮点技术有蜂巢能源的前驱体定向生长精准控制技术,通过控制前驱体合成参数,一次粒径放射状生长,打造离子迁移“高速公路”,提高离子传导,以及广汽埃安的石墨烯电池,石墨烯电池是将石墨烯与镍钴锰酸锂三元正极材料混合制成,石墨烯形成一个近似球面的三维结构,它能很好地与三元正极分子结合,增大相互之间传递电荷的面积,从而提升电荷传递效率,将充电速度加快至8分钟充满80%,这款电池将搭载在AionV上。
负极材料是充电倍率突破的重要方向,宁德时代在2019年曾对外宣称正在研发一种新的磷酸铁锂电池技术,在负极石墨的表面利用“快离子环”技术让石墨结构兼具超级快充和高能量密度的特性,石墨层增加锂离子嵌入速度后可以达到4C-5C的超级快充能力,相当于15分钟完成主要的充电过程;蜂巢能源在今年的上海车展上推出负极表面改性技术,采用液相包覆技术在石墨表面包覆无定形碳,降低阻抗,提升锂离子的通道。
电解液也需要较高导电率,并且不与正负极反应,能抗高温、阻燃、防过充。宁德时代引入了拥有超强运输能力的超导电解液,提升锂离子在液相和界面的传输速度,通过调控极片多孔结构的梯度分布,实现上层高孔隙率结构,下层高压实密度结构等。蜂巢能源采用含硫添加剂/锂盐添加剂等低阻抗添加剂体系电解液,降低正负极界面成膜阻抗,较高的锂盐浓度可以保证电解液较高的电导率。
在材料之外,还可以改善生产工艺来提高电池倍率性能,比如制备更均匀的浆料,提高涂布一致性可以使电极形成更均匀的导电网络,为离子传输提供快速通道。另外,将电极做薄也有助于提高脱嵌锂的速率,但矛盾的是,厚电极更有利于提高能量密度。因此,在目前的技术基础上,为实现快速充电,势必牺牲一定的能量密度,Taycan的电池系统能量密度约为148Wh/kg,作为对比,根据工信部的《新能源汽车推广应用推荐车型目录》,我国2019年申报数量最多的车型能量密度集中在160Wh/kg,2020年申报数量最多的车型能量密度集中在160-170Wh/kg之间,从某个角度来说,由于能量密度下降,Taycan车重增加了40多千克。
另外,说一句题外话,电池系统能量密度降低后,对于整车来说,更高的电压意味着更小的电流和更轻的线缆重量(Taycan的铜线减重4kg),在这个层面上来说,800V有助于整车减重。
我们知道单个锂离子电池的电压只有3-4V,电池串联后增大电压,并联后增大电流,因此为实现几百伏的系统电压,需要将电池进行串联,400V电压需要约一百个电芯串联,例如特斯拉Model 3短续航版的电芯总数为4416个,串联数为96;而800V则需要约200个电芯串联,保时捷Taycan的电池包总共包含396个电芯,串联数为198。
保时捷Taycan的串并联方式
保时捷Taycan是全球第一款量产的电压平台为800V的车型,其最高充电功率为350kW,电池包总重630kg,采用三元体系,总电量为93.4kWh,额定电压为723V,包含396个三元软包电芯,每个电芯的标称电压为3.65V,容量为66Ah;每12个电芯以6s2p的形式组成一个模组,模组电压为22V,容量为132Ah,396个电芯共组成33个模组。
上述33个模组串联,被分成两层放置,下层包含30个,上层包含另外3个,800A保险丝串联在18号模组和19号模组之间。在发生短路电流的情况下,将会中断高压蓄电池的供电,以保证电池安全。
上层模组的连接方式
串数增加,对电芯一致性要求提高
一致性,指的是用于成组的单体电芯的初期性能指标的一致,包括容量、阻抗、电极的电气特性、电气连接、温度特性、衰变速度等,如果电芯之间一致性存在差异,将影响整个电池组的性能。
从上面的分析可以看出,800V高压架构的Taycan的电池采用的是198s2p的连接方式,串联数为198个,较400V系统增加了一倍。对于串联回路,在充放电时流过的电流是一样的,因为电芯内阻的差异,单体电芯表现的电压不同。内阻比较大的电池在充电时会提前充满或优先到达上限电压,放电时则会提前到达下限电压,为了避免过充过放,电池管理系统就会截止充放电,而此刻其他电芯还未充满或充分发挥容量,从而导致电池容量的浪费。内阻高的电芯完全充放电的频率更高,使其衰减更快,久而久之,这颗电芯就更可能发生失效或安全故障。串数越多,电芯产生问题的概率就越高,对于电芯一致性的要求也相应提高。
目前,改进电池一致性的方法主要有:(1)极限制造:在生产过程中控制原材料的一致性、改良工艺过程及参数等,例如宁德时代就将极限制造创新列为自己的四大创新体系之一,将产品缺陷率由ppm级做到ppb级;(2)电池下线后即对电池进行筛选,选择同一批次性能相近的电池成组;(3)电池管理方面:在使用过程实时监控,优化电池的充放电、热管理等等,这个我们后面会讲。
电池热管理
为进行对比,我们假设存在电压为400V的电芯,将其分别组成电量相同,电压分别为400V和800V的电池包,则其串并联方式如下图:
目前国内充电桩支持的最大电流为250A,未来可达500A,若电流过大,将导致充电电缆过粗过重,给使用带来不便。因此,在外部输入电流一样的情况下,由于并联分流,流过800V系统单个电芯的电流将大于400V系统,相应的800V系统产生的热量也更大,对于热管理的要求越高。
我们来看一下Taycan的热管理,水冷板分别在电池箱体下侧,可有效隔绝冷却液与模组,提高电池安全性。由于模组分布在两层,其水冷系统也分为上下两层,共13个冷却支路,每个冷却支路有两根水冷管并联,水冷管采用口琴管的方案,每根水冷管有10个并联通道。
电池的液冷系统与整车的冷却系统是交互的,动力电池将热量传递给水冷板中的冷却液,冷却液再将热量通过热交换器传递给整车的冷却系统,最后将热量排放到空气中。
热安全方面,由于快充过程中产热量大,热失控的风险增加,因此需要进行有效的监控与预警,电池包的结构选材方面也要优化改进。
此外,800V高压快充技术对热管理的要求还体现在电池散热与升温之间的平衡:
一方面,由于通过单个电芯的电流更大,导致电芯产热更多——温度升高——加剧电芯老化/产生安全隐患——波及其他电芯甚至整车。另一方面,低温环境并不利于快充,热管理系统需要将即将进行快充的电池的温度适当提高,例如,Taycan电芯进行快充的最适宜温度为30℃,所以,车主如需要进行大功率快充,那么整车会事先将电芯温度调整到30℃,如果在充电时还没有达到这个温度或是车主没有事先设置进行加热,Taycan会首先将电芯加热到30℃,然后才允许大功率充电。
BMS
BMS对电池进行监控和管理,是动力电池系统的大脑。一般来说,BMS由一个主控单元和多个从控单元组成,从控单元直接连接动力电池,主控单元通过CAN总线或菊花链通信等方式管理多个从控单元。
上文我们提到,一个电池包中的电芯要尽量保持在一致的状态,BMS具有均衡管理的功能,即根据电芯信息,采取主动或被动的方式,尽可能均衡各电芯的荷电状态。BMS有两种均衡方式:主动均衡和被动均衡,主动均衡是将电量由SOC高的电池转移到低的电池中,结构较为复杂且成本高;被动均衡是将SOC高的电池的电量通过并联电阻消耗掉,这种方式结构简单且成本低,但是会造成能量浪费,目前采用较多的是被动均衡。BMS需要考虑电池自放电、均衡时间、散热等因素,来管理电池状态,使其保持一致,上文提到,串数增多,电池一致性要求也提高,同样的,对BMS的均衡能力要求也要提高。
再有就是, BMS中存在高压电路和低压电路,高低压电路之间的通信需要使用通信隔离芯片,电池包电池达800V后,这种耐高压的隔离芯片要重新选型,选择汽车级加强隔离的芯片。
除上述内容外,由于电压电流的变化,电池包内相关元器件、连接件等也需要重新选型,在此不再赘述。
来源:NE时代 (责任编辑:子蕊)
|