市场
从盈利能力来看,2017年锂电池铝塑膜价格约为31元/㎡左右,毛利率维持在55%左右。而由于新能源汽车补贴政策退出,国内锂电池厂商迫切要求降低锂电池原材料成本,因此未来三到五年内随着国产技术成熟,规模化生产形成优势,国产铝塑膜企业不仅具备较强的议价能力,市场容量也相当可观。
铝塑膜是我国动力电池国产化进程中的最后“一座城池”,也是动力电池“三剑客”之一的软包电池最与众不同的关键材料。在国家政策向高能量密度电池倾斜的背景下,软包电池的市场渗透率不断提升,铝塑膜的需求量也随之迅速激增。
但是,目前国内铝塑膜市场却大面积“沦陷”,核心技术受制于日韩,全球动力电池“老大”被捏住喉咙而仰人鼻息,成为目前行业中“不能承受之殇”。
“不能承受之殇” 随着越来越多的车企和电池厂商采用软包技术路线,铝塑膜市场呈现出了爆发式增长。数据显示,2017 年我国锂电池铝塑膜的需求量同比增长了47%,预计未来5年软包电池与铝塑膜的需求量将分别从26GWh和1.2亿平方米,增长至94GWh和2.8亿平方米,到2030年我国动力电池的需求量将达到459GWh,其中软包电池渗透率将达到45%,铝塑膜的用量也将增至8.3亿平方米。
虽然我国铝塑膜市场需求量巨大,但是令人“痛心疾首”的是,目前我国铝塑膜国产率仅不到10%,且主要集中在消费类3C锂电池领域。全球铝塑膜市场和技术一直被日韩等少数企业垄断,其中日本印刷株式会社(DNP)、日本昭和电工、日本凸版印刷株式会社(T&T),以及韩国栗村等企业,掌握着铝塑膜的核心技术并占据绝大部分市场,仅日本印刷株式会社与日本昭和电工所生产的铝塑膜在全球市场占有率就高达 70%。
据了解,我国高端铝塑膜高度依赖进口,国内市场被日韩企业垄断,铝塑膜价格居高不下,毛利率高达60-80%。对于数码类铝塑膜,国内有部分企业可以进行生产;而在动力电池领域,2017 年新能源汽车政策补贴大幅退坡,终端降成本压力进一步传导至动力电池等厂商,电池环节的压力加剧。目前铝塑膜成本占软包电池成本的15%左右,国内外产品价差约在20%~30%。国内锂电池厂商迫切要求降低锂电池原材料成本,因此铝塑膜实现进口替代、国产化需求日益凸显。
“差之毫厘,谬以千里” 目前,我国已成为全球最大的动力电池市场,也涌现出了世界级的电池企业巨头,技术实力也今非昔比,但是为何铝塑膜技术迟迟不能攻破呢?电池中国网了解到,铝塑膜由外阻层、 阻透层和内层三层材料组成,其指标要求很多,包括极高的阻隔性、良好的冷冲压成型性、耐穿刺性、耐电解液稳定性、绝缘性等,是软包电池中最关键、技术壁垒最高的材料。
业内专业人士表示,当前我国铝塑膜产品的性能,存在的主要问题是耐电解液和冲深不过关。国内铝塑膜的冲深在5mm左右,而国外可达到8mm,有的甚至达到12mm;厚度方面,国内铝塑膜最薄只能做到70μm,而日本铝塑膜最薄可以做到40μm。尤其是反应条件和精度控制,这种高精度的材料制造过程中,经常是“差之毫厘,谬以千里”,工艺控制的难度就体现在分毫之间。
从产品性能上看,我国铝塑膜产品与国外产品存在的差距还表现在:铝箔表面处理工艺落后、污染大;铝箔的水处理会产生“氢脆”,导致铝塑膜耐拆度差;铝箔表面挺度不够,良品率差;聚丙烯与高导热的铝箔表面复合时易卷曲,产生层状结晶;国内胶粘剂配方工艺较差,易出现分层剥离问题。
“知耻而后勇,闻利而争先” “知耻而后勇,闻利而争先。”虽然有着巨大的技术障碍,但是面对着惨淡的市场占有率,以及巨大的市场商机,铝塑膜产业必然要走向全面的国产化。电池中国了解到,国内企业实现铝塑膜国产化主要通过内生自主研发和外延并购两种途径。当前国内铝塑膜产品在性能质量上仍与国外高端产品存在差距,但相比之下具备性价比和销售上的优势,并且在不断完善技术和工艺。
据了解,国内的新纶科技通过收购日本凸版印刷株式会社的成熟铝塑膜资产,快速实现了向国内软包动力电池企业的导入,率先供应孚能科技、天津捷威等动力电池厂,形成先发优势。道明光学通过自主研发,成为国内极少数能够量产铝塑膜的企业之一,2017年度已获得超过30家消费类锂电池企业订单,动力电池客户正处认证中。明冠新材料2017年铝塑膜产能达3000万平方米,已经与天劲新能源、锂动电源等多家动力电池企业签署了中长期合作协议。
此外,紫江企业、璞泰来等企业也通过自主研发逐步进入消费锂电领域并获得订单,据悉,上海恩捷等企业正在筹划建设铝塑膜项目。软包电池的四大关键材料(正极材料、负极材料、隔膜、电解液)与方形电池及圆柱电池相比差别不大,其特别之处在于以铝塑膜为软包装材料,区别于方形电池及圆柱电池的钢/铝硬壳。
铝塑膜由外阻层(一般为尼龙BOPA或PET构成的外层保护层)、阻透层(中间层铝箔)和内层(多功能高阻隔层)三层材料组成,其指标要求很多,包括极高的阻隔性、良好的冷冲压成型性、耐穿刺性、耐电解液稳定性、绝缘性等,是软包电池中最关键、技术壁垒最高的材料。
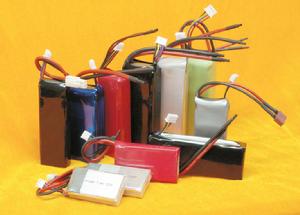
全球铝塑膜供给结构
软包电池因具有轻质、循环性能好及安全性能突出等优良特性,其市场尤其是动力软包电池市场在国内已开启放量,而其技术核心铝塑膜国产化率仍难破10%,国内软包电池在成本端仍受制于国外铝塑膜垄断龙头,国产化进程亟待加速。
国内多家企业已展开布局铝塑膜产业,此外亦有企业通过并购消化的模式切入铝塑膜市场。目前国内能够确认的产能约8000万平方米/年,但其中多数企业的产能利用率仍然极低。软包电池拥有能量密度高、重量轻、安全性高等多种优势,目前铝塑膜已经在日产聆风、雷诺、奥迪、通用、沃尔沃、北汽、长安、东风等国内外主流整车企业的新能源乘用车型中得到了广泛应用,并且其市场占比正在逐步提高。尽管国产软包电池的制造工艺和能量密度已经得到了极大的提升,但核心关键材料铝塑膜依然依赖进口,电池企业定价权较差,导致成本居高不下。因此迫切希望国产铝塑膜能够尽快提升产能性能替代进口,降低电池企业的成本压力。目前,国内铝塑膜市场90%依然被日本DNP、昭和电工、韩国栗村等日韩企业垄断,这意味着国产铝塑膜存在巨大替代空间。2016年国内锂电池铝塑膜市场需求量9500万㎡,国内铝塑膜产量达494万㎡,市场占有率已超5%,增长幅度超过50%以上。预计2017年,国内锂电池铝塑膜市场需求量将达12850万㎡,国内产量将达1200万㎡,国产铝塑膜市场占有率有望在2017年突破10%。
作为当前国内锂电产业链中技术壁垒最高、国产率最低、国产市场份额最小的关键材料,铝塑膜极度依赖进口、价格居高不下、对国产铝塑膜缺乏信心、国产铝塑膜产品性能亟待突破等问题已经成了当前废铝塑膜再生企业的心头之痛。一边是本土废铝塑膜再生企业的热切期盼,一边是市场需求的持续增长,软包动力电池关键材料铝塑膜的国产化已经势不可挡。在政策与市场的双轮驱动下,动力电池行业正从导入期向高速发展期加速过渡。而在技术路线上,国内已形成方形、软包、圆柱三足鼎立的局面,三种包装类型的动力电池已经在市场上逐渐找到了较为清晰的应用领域。其中,软包动力电池由于拥有内阻小,设计灵活,安全性高,重量轻等优势特性,能更好满足新能源乘用车高安全性、长续航里程、个性化设计等市场需求,受到了越来越多主流新能源整车企业的青睐。
然而,作为当前国内锂电产业链中技术壁垒最高、国产率最低、国产市场份额最小的关键材料,铝塑膜极度依赖进口、价格居高不下、对国产铝塑膜缺乏信心、国产铝塑膜产品性能亟待突破等问题已经成了当前废铝塑膜再生企业的心头之痛。在补贴退坡和上游原材料价格上涨的压力之下,废铝塑膜再生企业在2017年遭遇了来自上游材料涨价和下游客户大幅压价的双重挤压,降低动力电池制造成本成为了电池企业的重要任务。与此同时,自新补贴政策将补贴金额与电池能量密度直接挂钩之后,提升电池能量密度也成为了电池企业能否获得整车企业认可,甚至是能否参与未来市场竞争的关键。
在此压力之下,废铝塑膜再生企业发起了轰轰烈烈的提质降本运动,效果显著。在2017锂电供应链好产品动力电池全国巡回调研活动中,高工锂电在走访了超过60家废铝塑膜再生企业后了解到,电池企业在提升能量密度方面都取得了较大突破。其中,废铝塑膜再生企业的表现较为突出。包括桑顿新能源、孚能科技、国能电池、微宏动力、天劲股份、妙盛动力、中兴派能、多氟多新能源、捷威动力、上海卡耐、万好万家、新华电池、高佳新能源、遨优动力、超威创元、南都动力、恒宇新能源、冠城瑞闽、富朗特、鹏辉能源、亿鹏能源等电池企业,其软包磷酸铁锂电池单体比能量可达到160wh/kg,三元软包电池单体比能量达到200-240wh/kg,系统能量密度达到120wh/kg以上,达到最高补贴系数标准。
未来铝塑膜市场国产替代进口是必然趋势,国产开始得到了电池企业的认可,极高的性价比优势将为电池企业大幅降低成本,当前最重要的就是提升产品性能。而废铝塑膜加工企业作为高端铝塑膜缔造者,将充分利用公司的技术优势为电池企业提供优质铝塑膜,替代进口占据高端铝塑膜市场。我们在巡回活动中了解到,所有废铝塑膜再生企业都对国产铝塑膜持开放的欢迎态度,并对铝塑膜国产化取得的成绩表示认可,但在实际应用中却不敢贸然使用,更多的是小批量的测试,当前还是以DNP和昭和电工的铝塑膜为主。
明明对国产铝塑膜表示了认可,但在应用上却依然持保守态度,对于废铝塑膜再生企业对国产铝塑膜的“爱恨情仇”,连续参与了2016、2017年锂电供应链好产品动力电池全国巡回调研的铝塑膜制造商废铝塑膜加工企业深有体会。表面上看国产铝塑膜主要的竞争优势是价格,但是我们认为品质及稳定性才是目前国产铝塑膜的竞争要素,所以我们将会在保证生产效率、产品品质及稳定性的前提下进行降本、工艺升级,这样才能提高企业竞争能力、占据国内市场、建立国际品牌。
作为软包电池安全性的第一道防火墙,铝塑膜的性能直接关系着电池的产品品质,因此对铝塑膜的性能要求也非常严格。其中,极高的阻隔性、良好的冷冲压成型性、耐穿刺性、耐电解液稳定性、耐高温、绝缘性强是检验铝塑膜产品性能最关键的指标。业内人士认为,国产铝塑膜之所以迟迟无法大规模应用就是因为上述某些性能不过关,国产铝塑膜只有个别厂家的其中几个指标能达到DNP指标。例如,国产铝塑膜的密封性不过关,国内铝箔表面处理工艺落后,采用水洗除油和“铬酐”钝化处理,污染大。水有表面张力,铝箔微孔中的油处理不干净,造成后续复合工艺产生缺陷。水处理后的铝箔会产生“氢脆”,导致国产铝塑复合膜耐折度始终达不到日本水准。
同时,国产铝塑膜的冲深与日韩产品始终存在一定的差距。在厚度方面,国产铝塑膜的厚度也与国外的存在较大的差距。国产铝塑膜当前存在问题主要是产品的一致性和稳定性差,这就需要企业从制造工艺、设备和原材料等方面进行升级改进。针对这些问题,废铝塑膜加工企业设立了千级净化车间,室内生产温度严格控制在(23±2)℃、湿度(55±5)%,确保生产环境最优。同时公司引进成套日本生产设备,采用三菱、富士等一流元器件实现高精度生产,确保产品的稳定性、一致性和高品质。
在原材料方面,废铝塑膜加工企业采用热法工艺,不需要依附日本的CPP从而控制成本和品质,以高温粘结树脂层来粘合铝箔与PP热封层,产品具有优异的耐电解液腐蚀性。公司产品PP层厚度可调,可根据客户需求在一定范围内任意调整。关键还是废铝塑膜再生企业对国产品质信心仍不足,不敢贸然使用,使用的经验越少同时需要克服隐患担忧的时间也相对会较长,国产铝塑膜需要在外观一致性、热封性能、冲压成型性、耐电解液腐蚀性能等方面进行持续的改进和优化升级。废铝塑膜加工企业将不断完善产品品质,与上下游企业加强合作,研发生产出完全替代进口的国产铝塑膜,占据高端市场,对此公司非常有信心。
一个可喜的现象是,国产铝塑膜的产品质量已经得到了极大提升。在性价比、性能保障、市场交易灵活、售货服务完善等要素的保障下,国产铝塑膜的市场占比也在逐步提升。未来2-3年国产铝塑膜在国内的占比将有较大突破。
企业
中国锂电池铝塑膜贸易商分布
据)统计,中国铝塑膜贸易商有40家,主要分布在广东和上海地区,其中广东省28家,上海10家,两者合计38家,数量占比达到95%。
广东地区的铝塑膜贸易商集中的原因主要是A.珠三角地区是全国锂电池产业聚集地,下游客户集中。B.广东政府特别是深圳在税率政策方面相对其他地区有优势。C.地理位置优越,珠三角区域交通运输发达,物流成本低。
上海地区的铝塑膜贸易商集中原因主要是由于上海是中国乃至全球的经济中心。很多大型贸易公司都把总部设在上海,辐射整个中国区。
铝塑膜供应商分布分析
中国铝塑膜代理商,目前大都以代理进口铝塑膜为主。据统计,昭和铝塑膜的代理商数量最多有25家,其次是DNP有5家,栗村化学4家,凸版2家。其他厂商均为1家。 昭和和DNP的代理商数量一共为30家,占全部代理商数量的77%。
中国铝塑膜市场还是被日本垄断了绝大部分的市场,在进口铝塑膜品牌中一共有8家,日本占了7家。还有1家是韩国栗村化学。
国内真正深入锂电池外包装膜研究开发的厂家有新纶科技、上海紫江新材料、佛塑科技、江苏中金玛泰、东莞卓越、珠海赛纬等少数几家。由于投入资金巨大,课题难度较大,国内企业研究成果不多,除了新纶科技、上海紫江,企业企业几乎处于停滞状态,取得的成果和经验限于外层和中层部分,核心的内层材料仍然没有完全攻克。
目前已经实现量产的只有新纶科技、上海紫江、中金玛泰和佛塑科技,但是产品的性能与进口铝塑膜还是有较大差距,所以国内大部分厂家都还是在小批量试用阶段,不敢大规模采购。
铝塑膜厂商中国区代理商数量分布
昭和在中国区的代理数量是最多的,昭和电工在中国区设有销售子公司,昭光通商(上海)有限公司,昭和铝塑膜在中国70%以上的出货量是通过该公司售出。规模较大的一级代理商有:上海昭远、深圳昭洋和江阴宏大。其他为二级甚至三级代理商,这些代理商主要针对的是中小零散客户。大电池厂一般都直接从昭光通商采购。由于代理数量较多,昭和铝塑膜在中国的市场上流通的有不少是次品,这些次品大都是通过二、三家代理来销售的。有不少以次充好的现象发生。
DNP在中国区的代理商有5家。5家代理商互相独立运行,DNP对代理商的管控非常严格,代理商的客户必须经过DNP总部注册审核,已经注册的客户不能够再次注册,这种模式主要是也就是电芯厂如果想购买DNP铝塑膜,只能跟从其中一个代理商处采购DNP的铝塑膜,一旦登记注册之后,不能更换其他四家DNP代理商。这5家代理商各有特色,日商的大客户最多,主要客户有ATL、邦凯、TCL金能、北京国能、深圳金科、耀安、精进等。其中ATL现在在日商的月均采购量为200-220万平米,2015年最高时能达到250多万平米。盛永客户数量最多(中小客户为主),大客户有比克。梅特鲁--客户数量排第二;丸红---比亚迪,客户量最少,不超过5家。栗村化学有三家代理商。
数字
2017年,国内市场对铝塑膜的需求量已达16000万平方米,同比增长达45%;铝塑膜市场规模29.5亿元,同比增长39%。
国内企业生产的铝塑膜仅占总量的7%-8%,其余绝大多数依赖进口,国内市场份额几乎完全被日本DNP(约50%)、日本昭和电工(约20%)、日本T&T(10%-15%)和韩国栗村(约9%)化学四家企业瓜分。
软包锂电池由于在消费类产品中的高度适用性,总产量约占据方形、圆柱形及软包三种类别中的36.2%,2016年总生产量约为22.99GWh。
据了解,电池体积越小,单位电池容量铝塑膜用量将越大,动力电池铝塑膜用量约为150万平方米/Gwh,3C电池铝塑膜用量约为550万平方米/Gwh。
按照2017年到2020年国内软包动力电池和3C电池需求量,国内软包电池铝塑膜总需求在2017年约为1.25亿平方米,到2020年有望达到2.39亿平方米,由于3C电池单位电池容量铝塑膜用量显著高于动力电池,故3C电池需求处于较为主导的地位。
2017年,铝塑膜价格约为31元/㎡左右,毛利率维持在55%左右。2018年起铝塑膜价格如果每年下降5%,则到2020年价格下降到27元/㎡左右,2017-2020年市场合计也将达到230亿元左右。
结语
动力电池市场快速发展,对铝塑膜的需求不断增加,铝塑膜总需求量将持续增长。预计到2020年,中国铝塑膜市场规模将达到49.93亿元。我国铝塑膜市场需求持续扩大,而进口铝塑膜所需周期较长,导致我国铝塑膜市场出现阶段性供应不足的现象,国产铝塑膜的市场机会巨大。
(本网综合)
(责任编辑:子蕊)